History - Past and Present
The purpose of this particular page is to give a brief history of agriculture and describe current state of agricultural robotics and see some of the current work being done, because in order to see into our future, we need to peer into our past. This can help us imagine and create some of the innovations of the future.
The Brief History of the Past:
We believe that the earliest beginnings of what we call farming were in the area of mesopotamia, originating around the year 9500 B.C. E. Farmers were starting to select individual plants to harvest and grow [13]. Before this they only harvested wild cereals. They used only basic tools, some just chiseled rocks. Soon, farmers started specializing their crops to only a few species per farm. During the middle ages, farmers discovered how to create more intricate tools. Later, the Chinese invented the moldboard plow, which increased efficiency. [13]
Agriculture continued to grow from its small beginnings but did not change much for thousands of years. Farmers planted their fields by hand or with the help of plows or other non robot machines. The beginnings of robot machines really started in the late 1700's with the invention of the cotton gin.
Invented at the beginning of the industrial revolution, the cotton gin allowed for a more efficient cotton harvest. It was created by Eli Whitney in 1793 and got patented the next year [14]. It pushed along the industrial revolution and was a major breakthrough in agriculture. Today, gins are mechanized and controlled by computers and provide an extremely fast harvest.
The Present:
Today farmers harvest their fields with giant combines and other mechanized machines that use lots of gas and manpower and are not very friendly to the environment. They do provide for a quick harvest and are one of the reasons that agricultural productions has become more efficient.
Robotics is one of the fastest growing engineering fields of today’s industry. In several years, we might have robots that do our work, re-build themselves, and never require us to plug them in. Robots are just starting to appear in farms in the last 20-25 years. Most of the robots are still in development in universities and other research places and have not made a significant impact on farming ...yet. The future is bright and these experimental robots are paving the way for robot farmers in the near future.
This section will detail a few of the robots currently in use or being invented.
Automated Sheep Sheering:
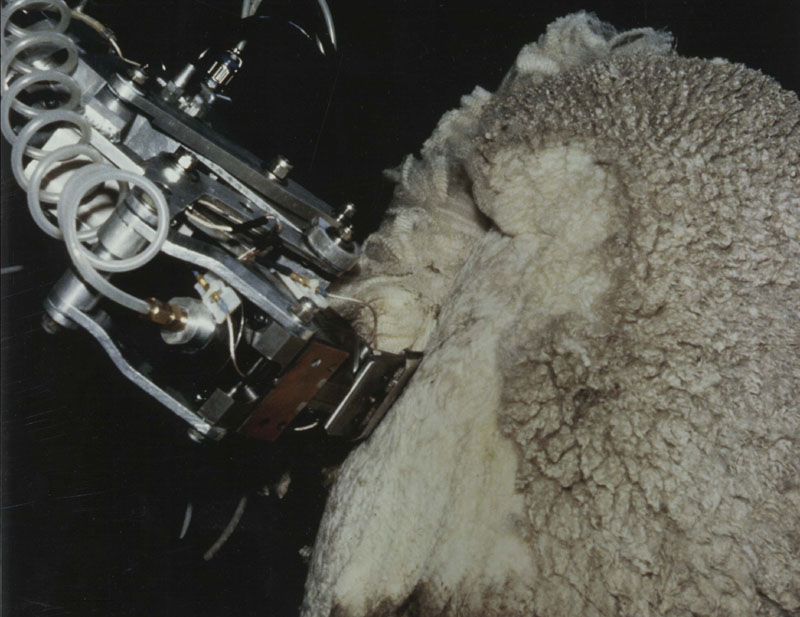 |
One of the first automated processes in agriculture to help farmers with tedious tasks was developed at the University of Western Australia in 1979 and is designed to sheer sheep. Sheep sheering is the process of taking the fur or wool of a sheep. This wool is then cleaned and used in the textile industry. The sheep is restrained and many sensors help to position the cutters so the robot does not hurt the sheep. The Oracle sheep sheerer was used as a test model to design its successor, the Sheer Magic Robot.[7]
The image at the left shows the Oracle sheering a sheep. The image was taken from http://www.mech.uwa.edu.au/jpt/shearmagic/autoshear.html |
Fruit Picking:
Automated fruit picking robots have been used in Agriculture since the 1980's and were one of the first robots to be used to harvest crops. These robots in fact, led to the development or lines of research today in automated crop harvesting. The robot is able to distinguish between leaves and ripe and unripe fruit through the use of a color camera [8] , like the XBC used in Botball. We plan to use a similar system in our own agricultural robot detailed on our solution page.
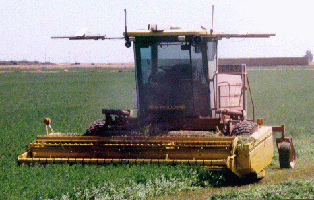
Image from: http://www.technovelgy.com/ct/Science-Fiction-News.asp?NewsNum=177 |
Demeter and Ag-Ants:
Engineers are building a wide variety of ‘agbots’, including the Demeter automated harvester (see below). This harvester isn’t fully robotic, however, because you can still control it manually. It does have a ‘cruise control’ and ‘drone’ feature. The first gives control to the harvester for a short period of time, and the latter allows you to remotely control several harvesters at once.[9] |
Ag-Ants:
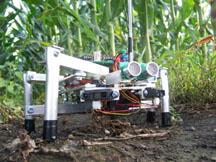
An Ag-Ant at work in the fields.
Image is from http://www.nasaexplores.com/show_912_student_sh.php?id=041007162029 |
There are several other agbots in production, though. One is the foot – long “ag ant”, which you could make a ‘colony’ of to have a large, co-operative task force. These ‘Ag-Ants’ work as a “hive” and do the function of huge and expensive pesticide sprayers and harvesters. ‘Ag-Ants’ actually look like ants as well. They have six robotic legs that allow them to crawl between the rows of crops and have many sensors and controls mounted on top. “Who needs 500 horsepower to go through the field when you might as well put a few robots out there that communicate with each other like an army of ants, working the entire field and collecting data?” says Tony Grift, University of Illinois agricultural engineer [10]. These ‘Ag-Ants’ are also very inexpensive. They cost $150 to build each one. When asked about how the robots worked and what was the plan for the future, Grift answered, “We're thinking about building 10 or more of these robots and making an ecosystem out of them," Grift said. "If you look at bees, they will go out and find nectar somewhere. Then a bee will go back and share this with the group and the whole group will collect the food. Similarly, one robot might find weed plants. Then it would communicate this location to the other robots and they would attack the plants together as a group--an ecosystem, if you will”. Grift also said that someday he would like to see an experimental farm run autonomously by robots[10]. |
Another robot, this one for roughly $500, has been developed as well. The robot is equipped with two ultrasonic sensors that bounce sound waves off of objects, as well as four of the cheap infrared sensors used in simple motion detection sensors. This one is (so far) simply designed to meander through the rows in a ‘drunken sailor’ style. It goes in a zigzag pattern, sensing a plant at the end of each ‘line’ and turning into the next ‘line’. [11]
The Future and Problems to Overcome:
The future of agricultural robots seems to hold small and inexpensive robots that can work efficiently. These robots work together as a team, passing information back and forth and solving problems in a hive type manner. The future looks to hold efficient robots that can spry herbicides and pesticides on to crops in an efficient manner so that pollution is kept to a minimum.
Currently the main problems in agricultural robots are:
-
How can the robots distinguish plants from weeds and other visual problems. A lot of work has been done with computer vision and but it is still not very good. In fact, Wikipedia describes the field this way "The field of computer vision can be characterized as immature and diverse" [15]. Scientist still have lots of work to do to get computer vision right. But we think a simple color and motion camera like that used in the XBC can go a long way to giving robot farmers "eyes". This is shown in our solution.
-
Navigation is also a problem. How can robots know exactly where they are? This problem is pretty easy to solve with GPS and in fact Tony Grift imagines robot farmers will use GPS: "Planting, seedbed preparation, spraying, cultivation are all possible with smaller robots using GPS guidance" [6].
-
How can they communicate this with others? Tony Grift imagines robots talking to each other and communicating all their information with each other to make farming more efficient. We also implement this in our solution.
-
How do they avoid destroying crops while moving from place to place?